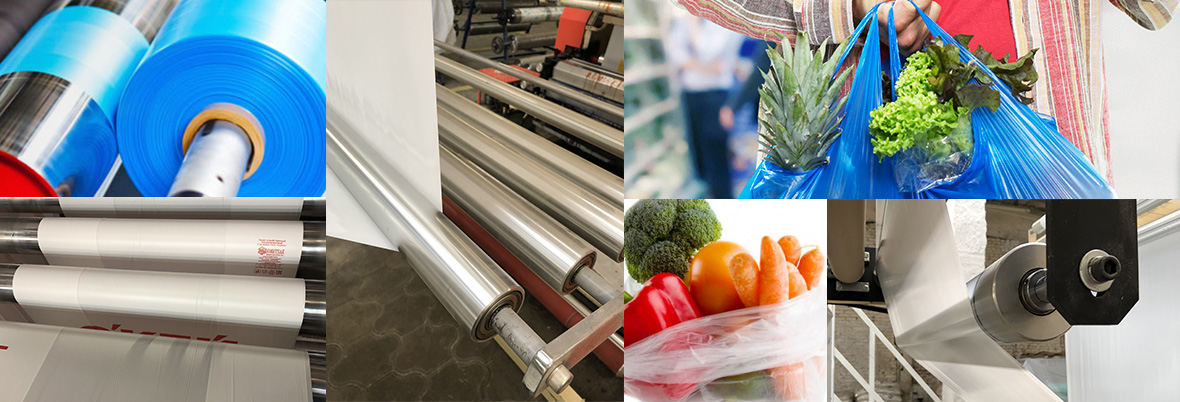
Производство
Использование современного и высокопроизводительного оборудования позволяет ООО «Юнитполимер» выпускать продукцию со стабильно-высоким качеством. Постоянное совершенствование технологий и рационализация производства в сочетании с высоким профессионализмом сотрудников исключают производственные сбои, дают возможность выполнять заказы в кратчайшие сроки.
Общая площадь производственных цехов составляет 6000 м.кв., на которых расположены экструзионные установки, пакетоделательные станки, печатные машины. Круглосуточная работа высокотехнологичных линий позволяют выпускать более 500 тонн готовой продукции в месяц.
Производственный цикл
Производственный цикл включает в себя следующие этапы:
1. Экструзия
Базовым сырьем для изготовления полиэтиленовых пакетов является гранулированный полиэтилен. Изначально он представляет собой маленькие прозрачные гранулы.
Экструзия – это процесс превращения гранулированного полиэтилена в пленку.
Специальная машина — экструдер – расплавляет гранулы, после чего расплав выдувается через тонкие щели. Пока еще горячая пленка, проходя несколько метров в воздушном пространстве, охлаждается и застывает, после чего сматывается в рулон.
Для того, чтобы вместо прозрачного полиэтилена «выдуть» белый или цветной, еще до расплавления в него добавляются гранулы красителя, называемого «суперконцентрат».
На выходе получается полиэтиленовый «рукав» или полурукав заданной толщины, ширины и цвета.
2. Флексопечать
На первом этапе флексопечати важную роль выполняет колеровщик. Его задача в том, чтобы приготовить для печати краски, точно соответствующие согласованным с Вами цветам. Краски смешиваются из большого числа компонентов.
При изготовлении пакетов методом флексографии, печать на них наносится до того, как получится пакет в привычном виде. На этапе флексопечати вышедший из экструдера рулон полиэтиленовой пленки подается в флексомашину. Флексоформы, наклеенные на печатные валы, оставляют на пленке отпечатки с заданной периодичностью. Далее отпечатанная пленка снова сматывается в рулон.
3. Вырубка, сварка, упаковка
После флексопечати рулоны пленки подаются в т.н. пакетоделательные машины. Тип машины и ее настройки соответствуют типу требуемого пакета. Здесь осуществляется сварка швов пакета, вырубка, приклейка (или приварка) ручек, формирование спаек или просто пачек пакетов. Остается лишь аккуратно, по возможности, не сминая, свернуть пакеты и поместить их в групповую упаковку.
Контроль качества
Сырье и материалы, поступающие на предприятие для изготовления изделий, подвергаются входному контролю по ГОСТ 24297.
Изготовленную продукцию предъявляют к приемке партиями. Каждую партию пакетов подвергают наружному осмотру, при котором определяют целостность упаковки и правильность маркировки.
Для проверки соответствия изделий требованиям настоящих технических условий проводятся приемо-сдаточные, периодические и типовые испытания.
1. Приемо-сдаточные испытания проводятся при работе каждой смены производства пакета в течение смены.
Для проведения контроля качества из различных мест партии пакетов случайным образом отбирают выборки и проводят контроль по соответствующим показателям:
- внешний вид пакетов, швов;
- геометрические размеры;
- толщина пленки;
- герметичность швов, пакетов;
- прочность швов;
- прочность пакета с ручками;
- слипание внутренних поверхностей пакета;
- качество нанесения печати;
- гигиенические показатели.
Результаты испытаний оформляются протоколом приемо-сдаточных испытаний контрольных образцов.
2. Периодические испытания проводятся на образцах, прошедших приемо-сдаточные испытания, с периодичностью не реже одного раза в двенадцать месяцев.
3. Типовые испытания проводятся при постановке продукции на производство, при внедрении и применении новых материалов, изменении технологии производства пакетов. При этом осуществляется контроль по всем показателям качества, указанным в данных технических условиях.